Polished Concrete
Polished concrete is practically everywhere, because it is one of the most durable and cost-effective flooring options. Retail stores, warehouses, manufacturing facilities, restaurants, schools, office buildings, and many more are choosing polished concrete for its practical advantages and decorative appeal.
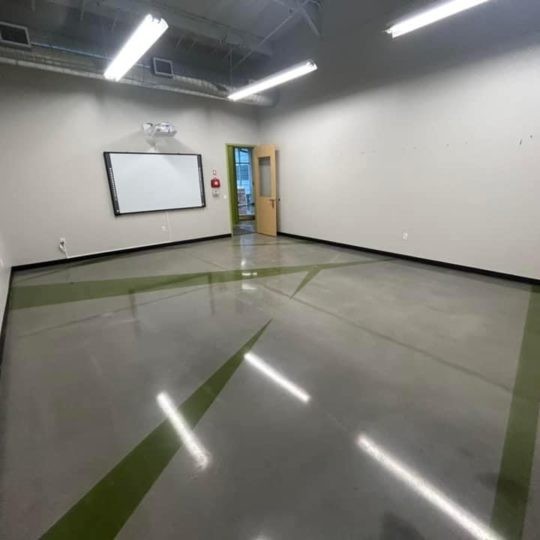
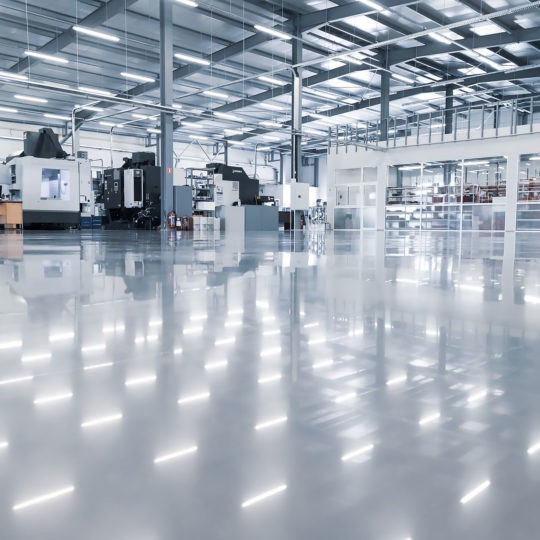
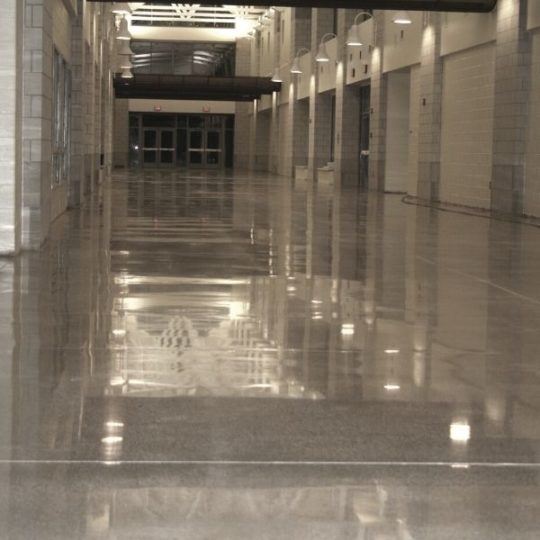
Advantages of Polished Concrete Floors
-
Durable
Polished concrete is extremely strong and durable, and is suitable for facilities with heavy machinery and foot traffic. Concrete has the longest life-span of all flooring materials, and has lower lifetime cost.
-
Easy to clean
Daily cleaning and maintenance is simple and cost-efficient, with no chemicals or waxes required.
-
Light reflectivity
The light reflectivity of polished concrete makes floors look brighter and reduces energy cost to light and color buildings.
-
No VOC & Reduced dusting
Improved air quality and appearance.
-
Sustainable design material
Polishing concrete translates into Reduced construction waste, compared to other flooring alternatives.
-
Unlimited decorative options
Polished concrete may be stained, stenciled or engraved. It is extremely versatile and customizable, with an endless array of decorative effects.
Frequently Asked Questions about Polished Concrete
Polished concrete provides an environment that is resistant to damage from chemical and oil spills, as well as, slip and water resistant.
Polished concrete is porous, so sealing it should prolong its life.
Experts recommend sealing concrete every 2-5 years to maintain its finish and prevent damages.
If water beads up on the surface, the floor has been sealed.
Although polished concrete floors are stain-resistant, they can still stain if spills are not cleaned promptly. Liquids such as fruit juice, wine, vinegar, laundry soaps, and urine can etch the surface of a floor, requiring repair. Standing water can also affect the sealer, and allow staining, making it less suitable for bathrooms.
Polished Concrete naturally draws its temperature from the ground rather than the outside so it tends to be warmer than tiles in winter and cooler than tiles in the summer.
Never use bleach, vinegar, or anything that is too alkaline or too acidic on polished concrete, because it will dull, etch and discolor the floor. Instead, use water or PH-neutral cleaner and a microfiber-style wet mop.
It is recommended to wait 24 hrs before walking on the floors, and a bit more before moving furniture.
Mechanically polished concrete can last many years, if it is properly installed and maintained during that time.
All concrete floors will crack, whether polished, coated, or untreated. Cracking is part of the initial curing process, and happens again over time.
Grind and Seal involves grinding the concrete, usually to 70-100 grit, exposing the aggregate according to the project spec, and then applying a topical sealer. It resembles the look of polished concrete but the gloss is achieved from a topical sealer.The process is simpler than concrete polishing, which involves more steps using progressively finer grits of diamond tooling until achieving the desired gloss or DOI. Polished concrete has a much longer lifetime expectancy than a grind and seal, and is much more durable, especially in areas with high traffic. High traffic floors need to be resealed periodically, which in the long run may become more expensive than polished concrete.
Burnished concrete involves using a high-speed burnisher to fill the concrete pores with a topical coating by heating and buffing the surface. The look is similar to polished concrete, and the process is less labor intensive and more affordable. However, a burnished floor is less durable than polished concrete and requires more maintenance.
Polishing Process
Here is a simple outline of the typical process steps in concrete polishing:
- Preparing the surface: Clean the concrete floor thoroughly to remove any dirt, debris, or coatings. Repair any cracks or imperfections in the concrete.
- Grinding: Use a concrete grinder with diamond grinding tools to grind the surface of the concrete. This step helps to level the floor and remove any existing coatings.
- Coarse grinding: Begin with a coarse grinding tool to remove imperfections on the surface. Work in sections and overlap each pass to ensure even grinding.
- Fine grinding: Switch to finer grit diamond pads to further refine the concrete surface.
- Polishing: Once the floor is ground to the desired level, proceed with polishing, using progressively finer grit diamond polishing pads. This part of the process provides a smooth and glossy floor finish.
- Concrete Floor Sealing: After polishing, consider applying a concrete sealer to protect the surface and enhance its durability.
- Maintenance: Regularly clean and maintain the polished concrete floor to preserve its appearance and longevity. Use appropriate cleaning products and methods recommended for polished concrete surfaces.
Concrete Finishes
Concrete floors can be processed or refined to a different level based on grit size and aggregate exposure.
Based on Grit Size:
- Ground concrete has a flat appearance with no or very slight reflection (below 50 grit resin).
- Honed finish has a matte appearance and/or slight clarity of reflection that has a low or medium sheen (100-400 grit resin).
- Polished finish has clarity of reflection and medium to high sheen.
Based on Aggregate Exposure:
- Cream polish – no aggregate exposure.
- Fine Aggregate or Salt and Pepper polish – usually requires starting with 120 grit metal tools to remove not more than 1/16 inch of concrete surface exposing fine aggregate.
- Medium Aggregate finish – usually requires starting with 70 grit metal diamond to remove not more than 1/8 inch of concrete surface exposing medium aggregate.
- Large Aggregate finish – requires 30 grit metal or coarser tool, such as bush hammers to expose large aggregate with no, or small amount of fine aggregate at random locations.
Diamond Tools
Understanding how diamond tools work is the foundation of grinding and polishing expertise. Most diamond tools are made of synthetic diamond powder, measured in microns and called grit, and a bonding material. The bonding material can be metal or resin, or a combination of bonding materials (hybrid tools). Metals are usually used in the first several grinding steps, whereas resins are used in the later polishing steps. Hybrids are also called transitional tools, and are used to remove scratches from metals before switching to resins.
Each consecutive grit step refines the floor and removes the scratches from the previous step. The rule of thumb is to double the grit with each step – 30, 70, 120, 200, 400, 800, 1500, etc. Skipping grits / steps can put you up against some serious scratched floor challenges.
Polished Concrete Maintenance
Polished concrete is easy to maintain, but it is not a maintenance-free flooring. Traditional daily maintenance includes mopping and auto scrubbing, but polished floors require more than that in the long run to preserve their shine. A maintenance program with SupraShine Floor Maintenance Pads will keep polished floors looking great for years to come.
We offer floor care solutions for a variety of floors, including concrete, terrazzo, natural stone, epoxy, overlays, and others. From restoration and deep cleaning to gloss upgrade and daily maintenance, SupraShine provides fast results with significant savings. No chemicals and no special equipment needed.
Selecting Equipment
Productivity depends on tooling as well as on the grinder size and weight. Be sure to consider the following questions before starting a job:
- How big is the project?
- How much time do you have to complete it?
- Is propane equipment allowed? Is there proper ventilation with fresh air access on the job site?
- Is power available on the job site and what voltage? Do you need a generator?
- Working wet or dry? What dust extractor is required for your grinder, if working dry? What slurry system can you use, if working wet?
- What are the pros and cons of propane vs. electric machines? Electric grinders operate more quietly, require less maintenance, and don’t need special air ventilation, as propane grinders do. However, they do require a power source, which is not always readily available on job sites and can increase your cost. Propane grinders on the other hand are cordless, easy to set up on the job site, and are often more productive due to higher head pressure.
Project Cost Variables to Consider
- Labor – the biggest cost in the concrete polishing industry.
- Abrasives and Equipment Cost (buy or rent).
- Floor Repairs, such as crack repairs and spalling along joints.
- Edges and handwork – if a lot of the edge work needs to be done by hand, your labor cost will go up.
- Samples – mock-ups take time and resources, but often help line up expectations.
- Utilities – if you don’t have the correct voltage on site, you may need a portable generator, which adds to the project cost.
- Work schedule – job deadlines and operating hours can affect labor costs.
- Dust and / or Slurry Disposal.
Concrete Polishing Training
Lavina Training Classes are a great way to start your concrete prep and/or polishing business. Training Classes are offered by most Lavina distributors at their locations. They usually cover everything from grinders and diamond tooling to different concrete finishes, concrete refining, and chemical applications. If you are new to the industry, try to attend several classes to learn more about equipment and job applications.